Enamel is essentially powdered glass which is fused to metal using extreme heat to create decoration. It has been used in varying forms for thousands of years to embellish jewellery and decorative objects and some of the earliest examples date from around 1400BC. There are a number of different techniques used in enamelling which all require specialist equipment and a good degree of skill.
I have outlined some of the main techniques below:
Cloisonné Enamel – Enamel is used to fill a series of metal enclosures which are soldered to a metal surface. Powdered enamel is placed into the enclosures, fired and polished to create a smooth, level surface.
Champlevé Enamel – Enamel is placed in channels and troughs which are gouged out of a metal surface. Each channel is separated by a narrow ridge. Enamel is placed into each recess in powdered form, fired and then polished to achieve a flat surface, level with the metal ridges.
Basse-taille Enamel – Developed from champlevé technique, but the flat recesses are replaced with engraved and carved depressions depicting scenes and more complex designs. Translucent enamel is then used to flood the design creating rich, tonal effects.
Email en ronde bosse (encrusted enamelling) – Enamel is used to coat 3-dimensional figures or objects.
Painted Enamel – As the name implies, wet enamel is used to coat a thin metal surface to provide a surface on which to apply subsequent layers to create a picture.
Plique- a –jour Enamel (letting in daylight) – This is one of the most challenging forms of enamelling and involves the creation of a mini stained glass window effect. Metal enclosures are created and filled using a temporary backing plate which is later removed allowing light to shine through. It is a technique which can create some of the most beautiful results, but has an extremely high failure rate due to its complexity.
Not surprisingly, over the years manufacturers have developed a range of alternative ‘Enamelling’ products which can go some way to achieving the look of traditional enamel, without many of the pitfalls.
Cold Enamel – Cold enamels come in powder or liquid form and require little or no firing. Powders such as Efcolor are worked in a similar way to traditional enamels but only require a low heat to melt which means they can be fired in a conventional oven rather than a kiln. The colours are very strong and don’t change during heating. Liquid cold enamels are usually made from epoxy resin and comprise of a coloured base and a separate hardener, which when mixed together form a solid layer. This type of enamel requires no heat to dry and will cure completely in approximately 24hours. Care needs to be taken as with all resins and some will exude strong fumes so it’s advisable to use them in a well ventilated area. There are a wide range of epoxy enamels available on the market meaning an infinite number of different effects are possible.
The joy of some of these more modern enamels is that they can be used on materials other than metal which makes them extremely versatile. However, you are unlikely to achieve the more delicate subtleties that traditional enamelling can achieve. I think it’s safe to say that all enamelling products have their pros and cons but patience and practice will ultimately pay off as the results can be stunning.
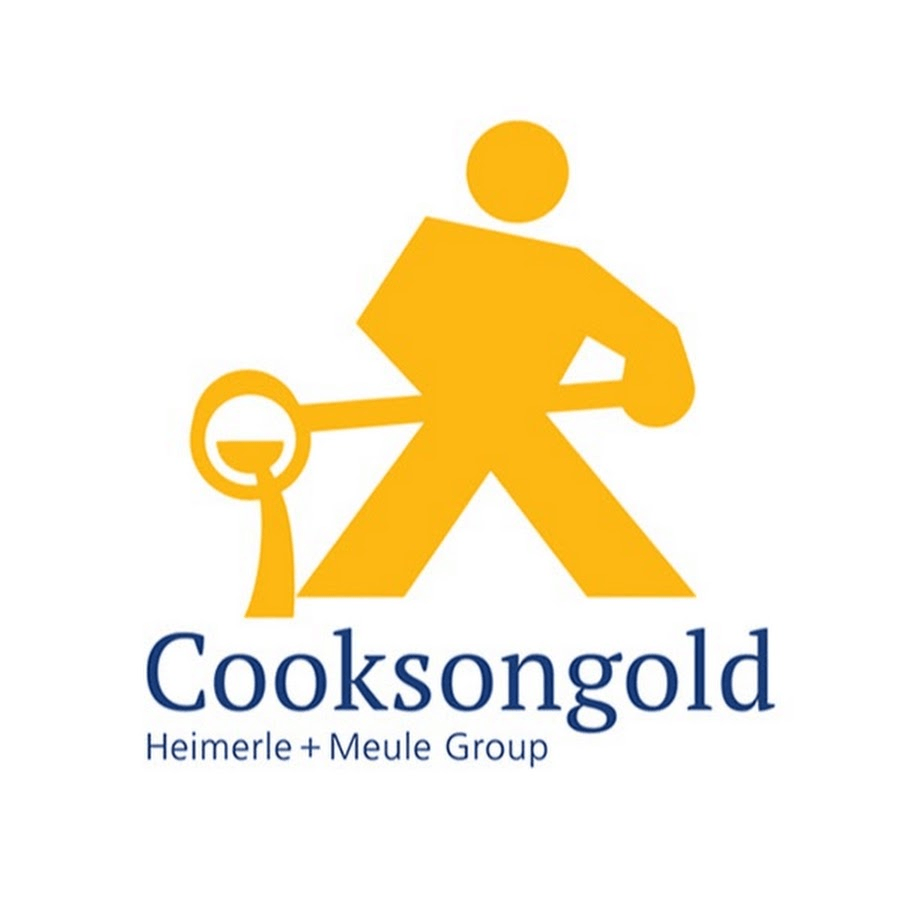
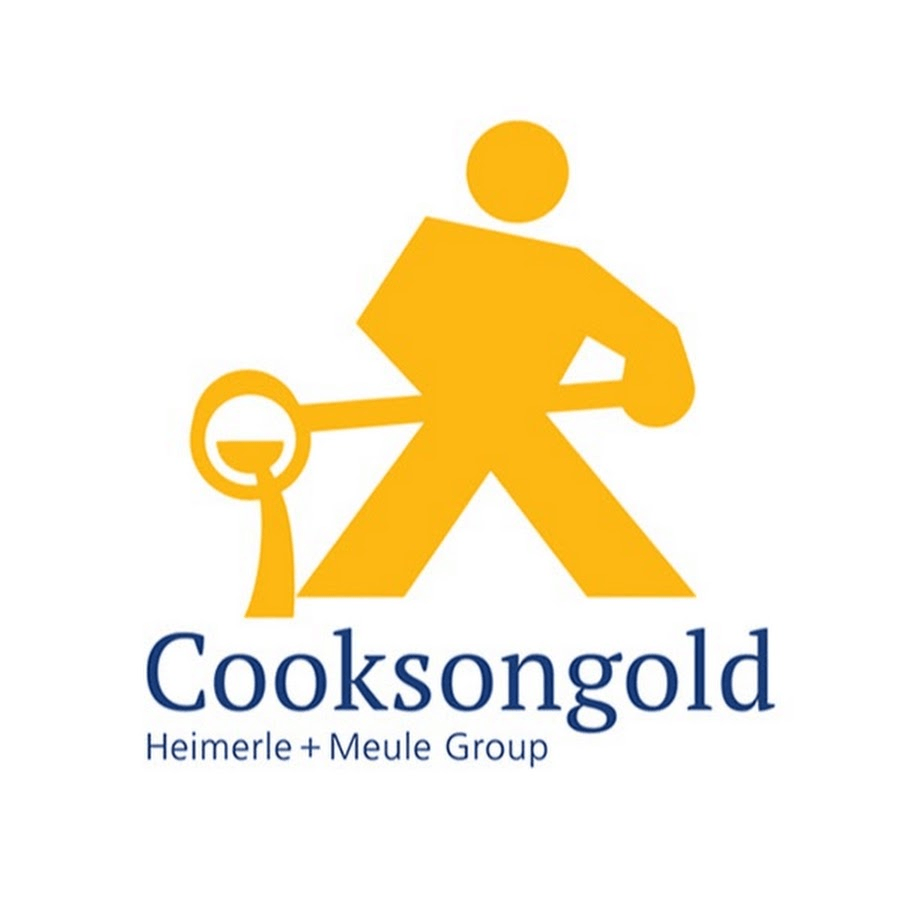
Cooksongold