When working with precious metal clay, choosing the right heating method can be a challenge, especially when weighing the benefits of torch firing versus kiln firing. Both approaches have their advantages and disadvantages and the best choice often depends on the specific needs and resources of the jeweller. Here’s a look at the pros and cons of each method to help guide your decision.
Torch Firing
Pros of Torch Firing:
- Affordable: A butane torch is relatively inexpensive compared to a kiln, making it a more accessible option.
- Portable and space-saving: Unlike a kiln, a torch is small and easy to store, making it ideal for jewellers with limited workspace.
- Quick setup: Torch firing requires minimal setup time. It heats up quickly and doesn’t require the preheating or cooling time associated with kiln firing, allowing for faster turnaround.
- Great for small projects: Torch firing works well for small pieces, such as earrings, pendants and charms, which don’t require prolonged heating.
Cons of Torch Firing:
- Limited control over temperature: A torch lacks precise temperature control, making it challenging to reach and maintain the ideal firing temperature. This can increase the risk of over-firing or under-firing the clay, potentially affecting its strength and durability.
- Not suitable for large pieces: Larger items or intricate designs that require uniform heating are difficult to fire with a torch, as it may not distribute heat evenly across the piece.
- Requires a steady hand and experience: Torch firing can be more physically demanding, requiring a steady hand and an eye for colour changes to gauge temperature. It may take some practice to achieve consistent results.
- Potential for cracking: Without the even heating provided by a kiln, there’s a greater chance of the piece cracking or becoming uneven due to rapid or uneven temperature changes.
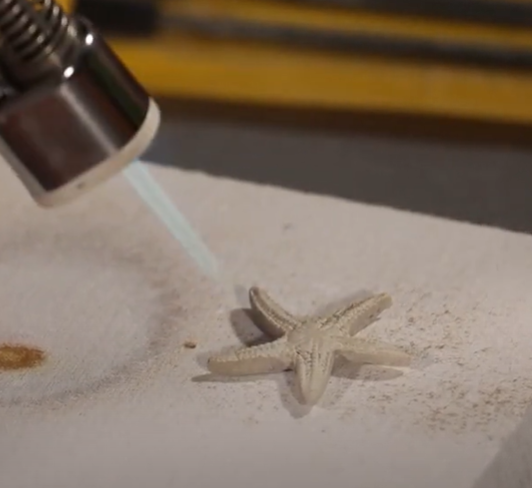
Kiln Firing
Pros of Kiln Firing:
- Precise temperature control: A kiln allows you to set and maintain a specific temperature, ensuring consistent and optimal results. This precision reduces the risk of under-firing or over-firing, producing stronger and more durable pieces.
- Even heating: Kilns provide uniform heating across the piece, which is essential for larger items or designs with intricate details. Even heating minimises the risk of warping or cracking.
- Time flexibility: Many kilns have programmable settings enabling jewellers to set up a firing schedule, allowing them to work on other projects while their piece is firing.
- Suitable for complex projects: Kilns are versatile and can handle larger or more intricate pieces, making them ideal for jewellers looking to expand their range.
Cons of Kiln Firing:
- Higher initial cost: Kilns can be a significant investment, which is a big investment for jewellers who don’t work with silver clay on a regular basis.
- Requires space: Kilns are larger and need dedicated space, which may be a issue for those with limited work areas.
- Longer heating and cooling times: Kilns require preheating, and pieces need time to cool inside the kiln after firing. This process can take longer than torch firing, which may be a disadvantage if you need a quick turnaround.
- Less hands-on control: With a kiln, there’s less direct interaction with the firing process, which some jewellers may find less satisfying compared to the hands-on approach of torch firing.
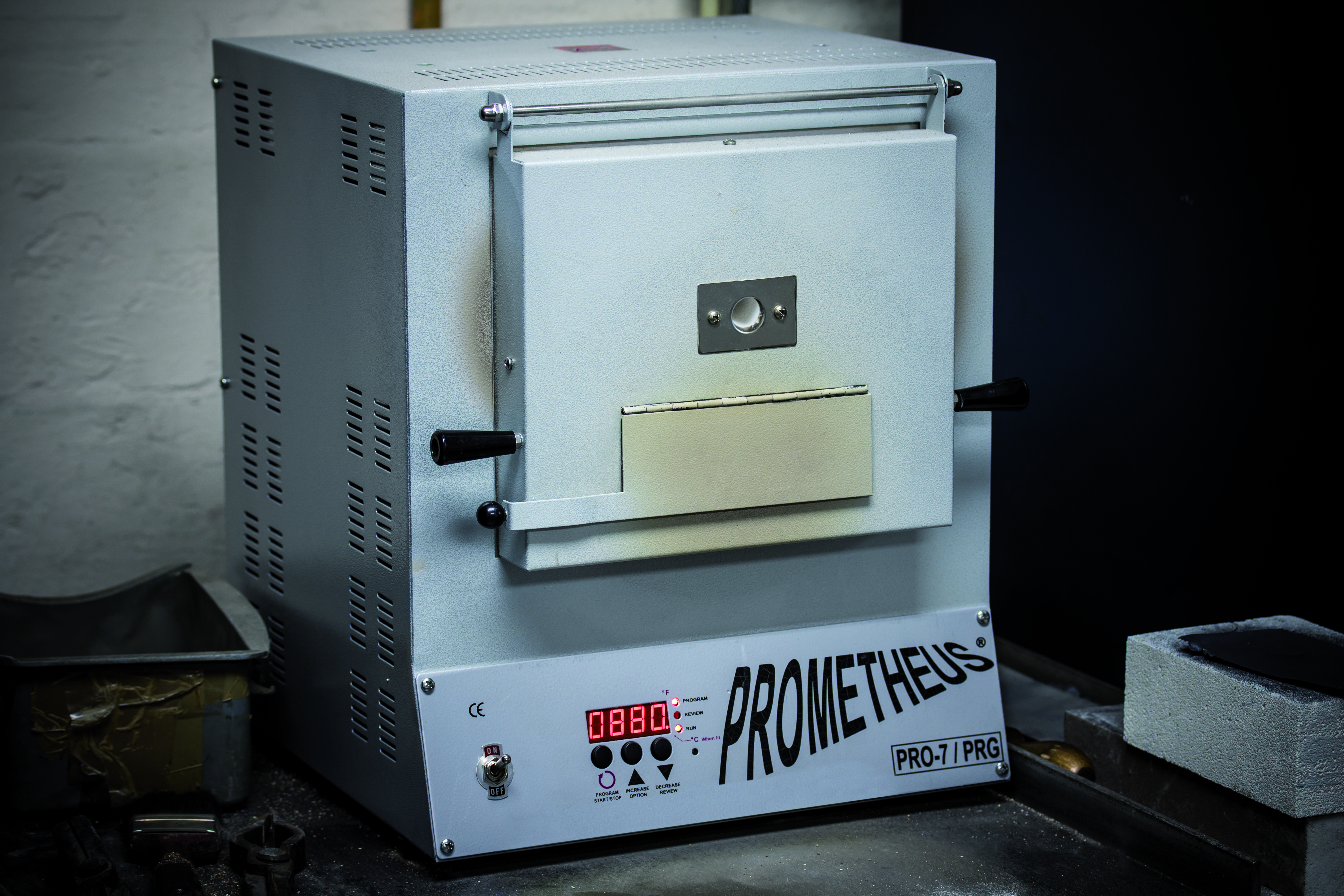
Both methods offer advantages and many jewellers choose to incorporate both into their practice. Start off with torch firing and upgrade to a kiln as your skills and projects grow. Ultimately, experimenting with both can help you discover which method suits your style and needs best.
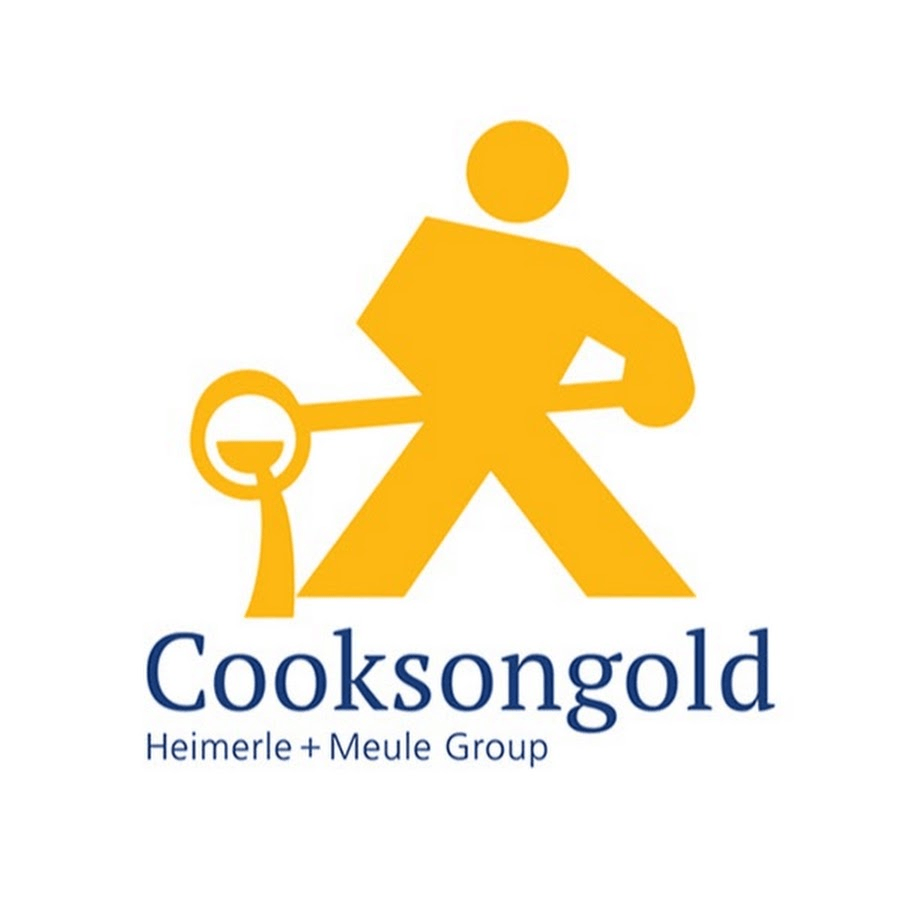
Sian Brown
Sian has been hand making her award winning jewellery in the West Midlands for over 12 years. Sian spent 10 years in Birmingham’s historic Jewellery Quarter before relocating to a quiet Worcestershire village.