Rhodium plating is a specialist process used to give jewellery, like white gold, a bright, tarnish-resistant finish. Using electroplating, a thin layer of rhodium is applied to the surface of the jewellery, improving reflectivity, scratch resistance and overall wear.
This guide outlines the full process using an electroplating unit. It covers the equipment required, how to prepare your jewellery and the correct procedure to ensure a smooth, professional quality finish.
What You’ll Need
Set up your workspace with the following:
- Electroplating unit
- Rhodium plating solution
- Degreasing solution (made with electrolytic cleaning salts)
- Acid dip (such as sulphuric acid or activator)
- Steel anode (for degreasing)
- Platinised titanium anode
- Copper wire or plating jig
- Distilled water
- PPE: gloves, goggles, apron, ventilation
- Optional: immersion heater
- Optional: extractor and filtration unit for fumes (e.g. 998 H003)
Tip: Make sure the jewellery is thoroughly cleaned and finished to your desired surface quality before beginning.
The Plating Process
1. Pre-Clean
Use an ultrasonic cleaner or warm soapy water to remove any grease, polishing compound or dirt. Rinse well with distilled water and allow to dry. Any contamination will affect the final finish.
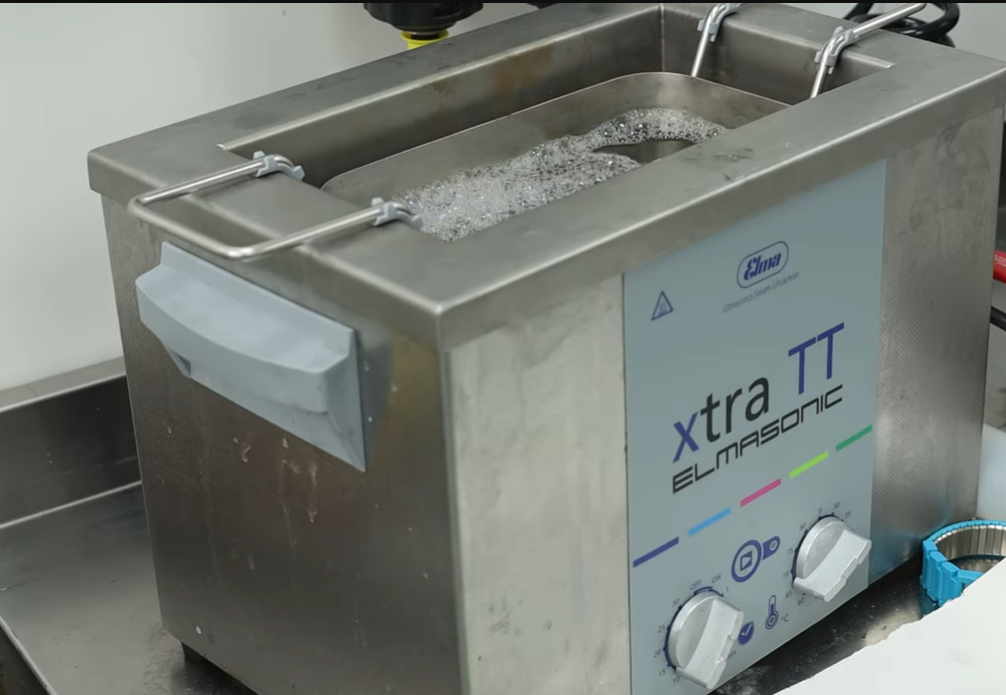
2. Prepare the Plating Unit
You’ll need four separate containers:
- Degreasing solution: mix up to 5 tablespoons of degreasing salts into distilled water until fully dissolved
- Acid dip
- Rhodium plating solution
- Final rinse (distilled water)
Insert the correct anodes into the appropriate baths. Secure the jewellery onto a jig or copper wire.
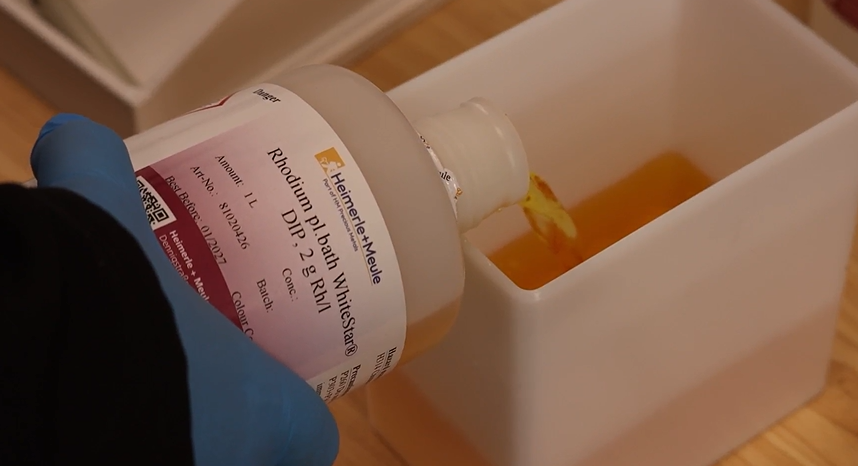
3. Heat Solutions (If Required)
If your degreasing solution or rhodium plating bath needs heating, use the immersion heater and thermostatic control. Check your solution’s datasheet for correct temperature ranges.
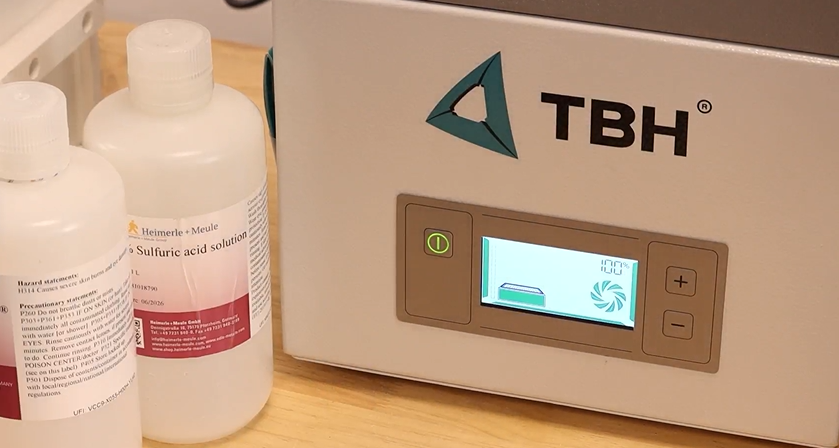
4. Degreasing
Place the jewellery in the degreasing bath and apply a current. For our solution, set the temperature between 20–30°C and the voltage between 4–5V. Submerge for around 30 seconds. Once complete, rinse immediately in distilled water.
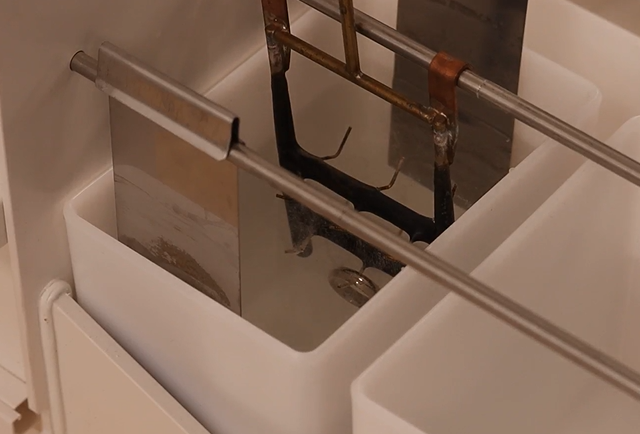
5. Acid Dip
Transfer the jewellery into the acid dip for 30 seconds to 1 minute. This removes any oxides and activates the surface. No power is usually required unless you’re using an electrolytic activator. Rinse thoroughly with distilled water.
6. Rhodium Plating
Submerge the jewellery into the rhodium plating solution and connect it to the cathode (negative terminal). Place the platinised titanium anode into the bath, ensuring it remains submerged but does not touch the jewellery.
Apply power — typical rhodium plating operates between 1.7V and 2.2V. Plating time is approximately 2 to 3 minutes depending on the desired coverage and solution type. Gently agitate the jewellery throughout the process using the cathode rod to prevent bubbles and ensure an even coat.
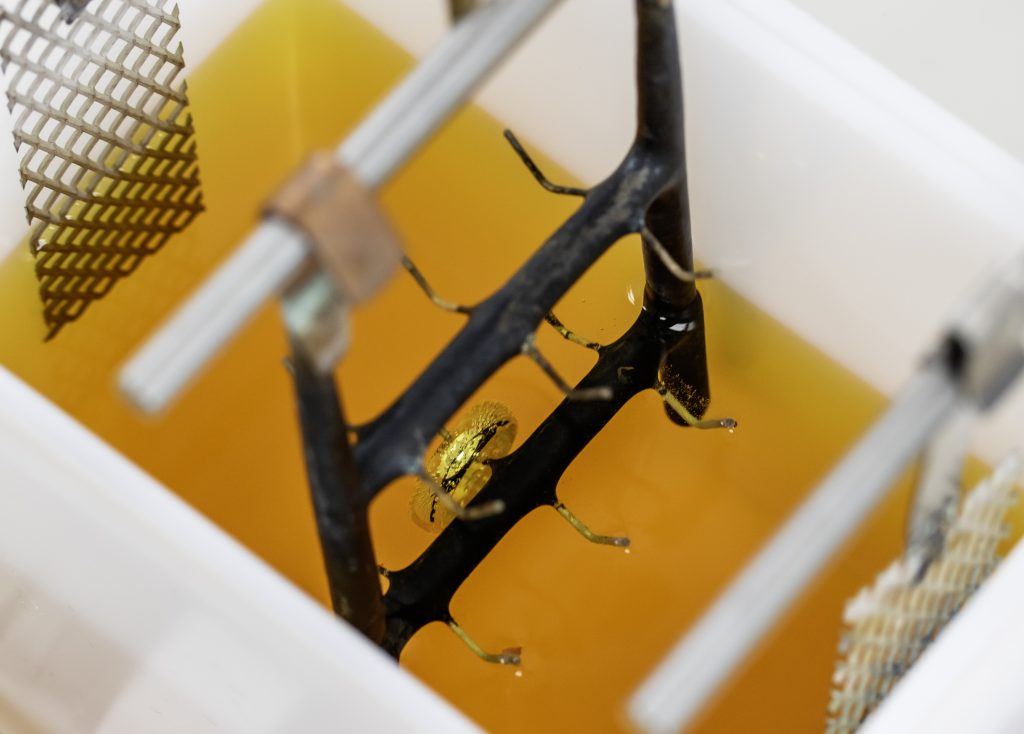
7. Final Rinse and Inspection
Once plating is complete, place the item in a clean distilled water bath to rinse thoroughly. Remove and dry, then inspect the surface. A well-plated item will show a bright, consistent finish.
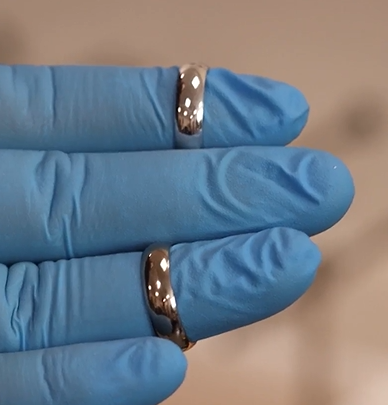
Tips for Better Results
- Always handle cleaned jewellery with gloves to avoid contamination
- Rinse well with distilled water between every step
- Use separate tweezers or holders for each solution to keep baths uncontaminated
- Check electrical connections are secure and consistent
- Monitor voltage and current using the LCD rectifier display on your electroplating unit
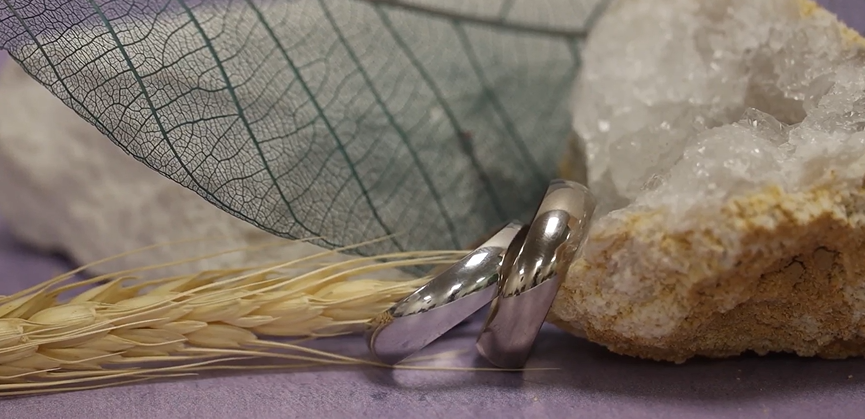
With the correct setup and a careful, step-by-step approach, rhodium plating can offer a high-end, mirror-like finish that enhances both the look and wearability of your jewellery. It’s a process for jewellers looking to achieve fantastic results.
For more information on our electroplating equipment and solutions click here
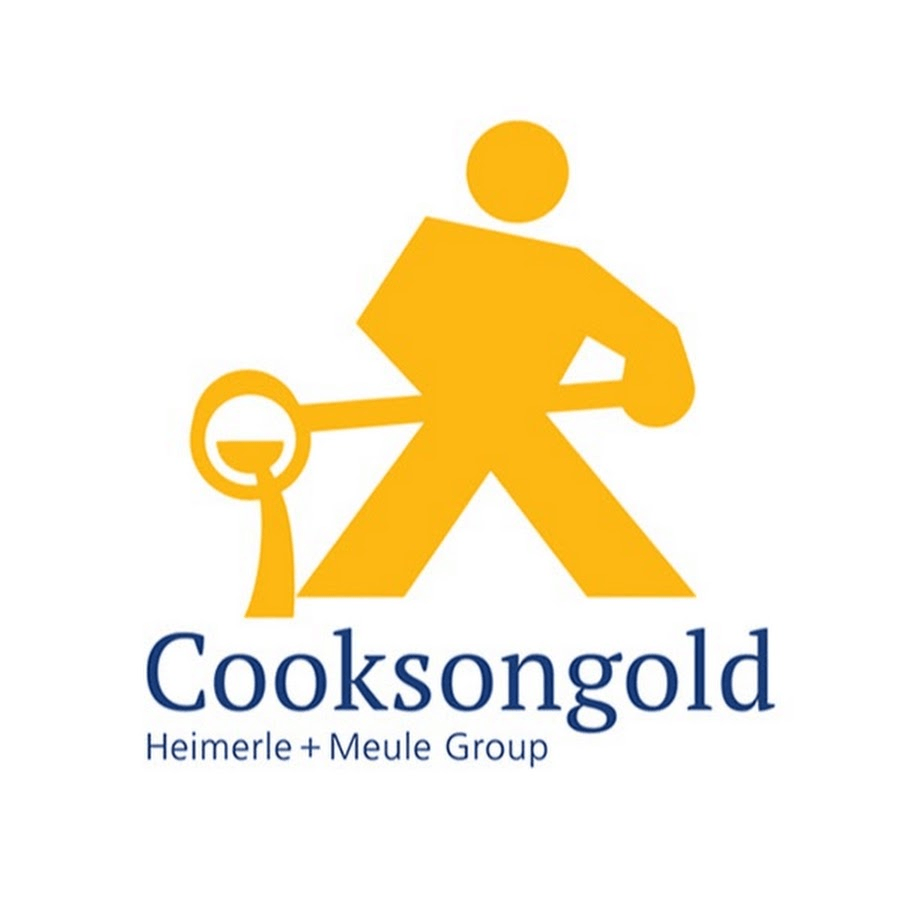
Sian Brown
Sian has been hand making her award winning jewellery in the West Midlands for over 12 years. Sian spent 10 years in Birmingham’s historic Jewellery Quarter before relocating to a quiet Worcestershire village.