Kit out your jeweller’s bench step by step…
In this series of blogs, we’ll explain how to make a jeweller’s bench work for you, with the supplies and tools required to get you started in your new jewellery-making workspace. Arming you with all the beginner jewellery making tools required to set up your workbench, and guiding you on how to create a comfortable spot for your upcoming jewellery making projects.
Beginners jeweller’s workbench essentials

Your jeweller’s workbench is the birthplace of all your projects, and where you’ll spend a lot of your time pouring over new techniques and tools. This is exactly why it’s important to make sure that your workspace is kitted out with the tools that you’ll use and set up for the way that you want to work. Whether you’ve decided to begin making jewellery at home, or have a more professional studio set up, here are the key jewellery making supplies you’ll need, and the considerations you’ll need to make as you set up your first jeweller’s bench.
Your jeweller’s workbench
A solid jeweller’s workbench should feature a semi-circle cut out of the front of the bench, leaving you with ample amount of space to work in, especially when you’re working on intricate projects. It should also feature a lip around the edge of the workspace – which prevents small tools or supplies from falling off. But the most important consideration you’ll need to make before purchasing a jeweller’s workbench is its height. A good jeweller’s bench should sit between 90 and 100cm in height. This is slightly higher than standard table so that you’re not in a hunched position as you work on your jewellery making projects.
Workbench seating
Once you have your first workbench assembled, it’s advised that you choose a chair that is adjustable. As the bench will be higher than a standard table, adjustable seating will ensure that you’re working at eye level with the surface of the bench. There may be instances where a higher position is more beneficial, so a comfortable office chair may be the best option. Finding the right height for your working position may take some time, but it’s relative to the way that you work and also the jewellery making projects you are undertaking, so take the time to find the right chair at the right height.
The right jeweller’s bench skin
Also known as a bench tray, the bench skin should sit underneath the semi-circle but out of your bench. This is used to catch any debris as you’re sawing or filing, and acts as a safety precaution in case you drop any hot metalwork or other supplies. Invest in a fire-retardant jeweller’s bench skin as an added precaution when working with hot precious metals. Metal scraps and dust caught in your bench skin when filing can then be recycled. Also referred to as ‘lemel’, you can collect the precious metal debris and return it to Cooksongold so that it can be refined and re-used.
Choosing a bench peg and clamp
A bench peg and peg clamp are vital tools for jewellery making beginners. The bench peg is a tapered wooden block A bench peg and peg clamp are vital tools for jewellery making beginners. The bench peg is a tapered wooden block which is then attached to your jeweller’s bench using the peg clamp. Bench pegs and clamps are often sold together and are easily attached to your bench using a G-clamp mechanism. The purpose of the bench peg is to provide you with the necessary support you need to apply pressure to your work, making it much easier for you to grip and work with your chosen material. It is often advised that a small v-section is cut into your bench peg – this facilitates better access to the material you’re working on and provides additional support as you file or cut precious metal pieces.
Getting your workbench light right
Lighting should be carefully considered as you set up your jeweller’s workbench. How is the general lighting in the room? Will you need to supplement it with dedicated lamps for your workbench? Even if the general lighting in your workspace is good, it’s worth investing in a workbench spotlight for use with intricate jewellery making projects. It will certainly help you to identify inconsistencies, such as small patches of fire scale, or details that you want to improve in your work.
Using a lamp that can be easily adjusted and angled will help you to avoid casting unwanted shadows across your workspace. Consider using a lamp that also features a dimming setting – this will help significantly when soldering as it will allow you to accurately see when the metal which you’re working on has reached it’s optimum temperature.
Looking for further advice on building out your workspace with vital tools? Discover our Beginner’s Guide to Jewellery Making Tools for in depth advice on your workshop essentials.
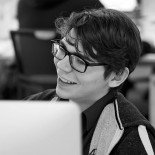
jaskcreative