-
I understand when you have the wax you make the mould from plaster of paris... but then two questions, does the wax run easily out of the mould when you heat it and is that what you use the furnace for? Secondly does the metal run easily into the mould without a centrifuge or does it cool too quickly and cause problems?
My bench was adjacent to a casting room, they had it all down to a fine art but the only time I have cast anything was cuttlefish style and though I know it wasn't complicated I can't remember what I cast except that it was small and simple. The idea of carving/modelling some stuff out of wax really appeals to me.
-
Hi Davey
Thats lost wax casting which is a bit more complicated and quite a lot more expensive to set up.
You need a burn out furnace to melt the wax out and a kiln or other manner of heating the metal to temperature for pouring- about 1100 C for silver.
Plus you get air bubbles in the investment plaster so have to use a vacuum table for that and either a vacuum or centrifugal unit to prevent them in the metal.
Nick has started a thread on here about equipment and Josef does a fair bit of lost wax casting so look out for his threads too.
Ive only done Delft clay and cuttlefish casting myself so far.
With Delft clay you press the wax model in, make an imprint and then remove before pouring the molten metal.
I don't generally have a problem with air bubbles but you can't cast anything like as fine as you can with lost wax and there is more clean up.
On the plus side its relatively cheap to set up and easy to do plus you can reuse the wax as often as you like.
Wax carving is fun
-
Thanks for the explanation. I am aware of the process of lost wax on an industrial scale, I was trying to imagine it on a small scale without such equipment. In which case it probably doesn't work so well...
The clay method as you have described obviously has its limitations but for shapes such as that thistle it has proved its usefulness
-
Hi Sarah & Davey
I think the Andrew Berry video is just up in YouTube land now here: https://m.youtube.com/watch?v=u5iAOkZgzLw it's very impressive the finish he gets just from the casting for that simple shape! I guess Sarah you got the kiln as an alternative to just heating the metal with a torch in a crucible like he does (which looked terrifying!)?
Faith
-
Hi Faith
I started off trying to melt the metal in a crucible with my Sievert but couldn't get it to flow, not sure why as I know some people do it that way, but as you say its pretty scary anyway! so I got a small kiln for about £500.
FAR less scary lol!
-
Davey
Lost wax casting works perfectly on a small scale, Josef makes some seriously detailed pieces.
Its just that the initial set up cost is pretty high so most people send it away.
-
When I say "small scale" I am referring to limited budget, IE no expensive equipment.
Excellent video, much better than using cuttlefish I think.
-
I don't know, definitely for some things but Nick put up a vid a couple of days ago of some bezels he had cast in cuttlefish which gave a much better result than you could get in Delft clay as the cuttlefish holds itself together better.
So both are useful I think, I must get some cuttlefish and try again as my first and only attempt was a total fail lol.
-
I cant remember what I cast but I remember distinctly scoring the edges to get it lined up, carving a channel after pressing the shape in and wiring it all together before pouring in the metal from a crucible. It was successful but required lots of cleaning up after unlike the finish on the front of that heart which was near perfect.
-
Yes I think the surface detail is much better replicated in Delft clay, I use it a lot for making custom horse pendants like this and its great for those.
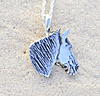
Its just if you want something with a small hole like a bezel as it doesn't retain that sort of shape well.
Posting Permissions
- You may not post new threads
- You may not post replies
- You may not post attachments
- You may not edit your posts
-
Forum Rules
Bookmarks