-
Polishing questions
I have a silver bangle about 1cm width which I managed to firestain quite badly (before I knew such a thing even existed). I polished the firestain out but then soldered on five settings for cabochons. Although I used some stinky stuff (with meths) to protect the bangle whilst I was soldering on the settings, the firestain has returned and i need to polish it out before I set in the stones. My tutor has said to get calico and wool mops for the pendant motor, and goats hair if I can get it; i can see the little calico and wool mops on the Cookies site, but there are lots of other attachments available too, some of which look like the may be better at getting in the smaller spaces between the bezels. Any recommendations other than the calico and wool mops? Will I need more than one of each?
If all else fails and I can't get rid of the firestain, then could I resort to a satin effect or would this make the firestain patches look worse? Would I use a specific pendant drill attachment for this, bearing in mind I don't want to damage the bezel settings (someof them look a bit brutal) and as this is the first bezel set piece I've done I'd really like to not mess things up!
Thanks
-
Would the stinky stuff have been Argotect?
If there's firestain there, there are 3 possible approaches: Ignore it, plate over it, or physically remove it. I'm not very good at #1, #2 isn't an option I've used, so #3 is what I go for. This involves physically removing the metal - with scrapers, abrasive paper, Scotch stones/Water of Ayr stones (if you can get hold of them!), pumice wheels - whatever is suitable. Using a pendant motor I've had pretty good results using 3M radial bristle wheels, although the resulting surface can need some refinement - I find they can be a bit inclined to leave swirl marks.
One trick that Jesa & Al showed me was to use a piece of tracing paper to see firestain - rather than being distracted by the shiny finish, you can hold the tracing paper against the metal & see the dark splodges. I also find that dullish fluorescent lighting helps to spot it.
I'd probably not try for a satin finish until the firestain is gone, personally. Depending on the shape of your bangle, my first port of call would be wet & dry or Micromesh in a relatively coarse grit - 320 wet & dry, for example - backed with a suitable stick.
-
Well I’m the odd one out on this forum as I rarely polish anything to a high lustre, except for the occasional edge or highlight. To me polishing just removes all the attractive artist's marks, rather like putting glass over a painting.
The result is that fire stain is not a problem I get worked up about, because it is difficult to see with a matt finish. To achieve this try some of the following, but the best results are if you can succeed in keeping perfectly parallel strokes:
The coarsest radial wheels for the flex shaft, green Scotchbrite wheels on lathe or flexshaft, or those dark grey abrasive blocks filled with foam used by decorators when rubbing down. You can also get wild swirly patterns with wet coarse steel wool, with or without soap. Peter has also mentioned micromesh, but it needs to be quite coarse.
You need to experiment on cheap test pieces to decide on your favourite. The only thing I personally find dull is pumice or scouring powder.
Let us know how you get on, Kind regards, Dennis.
-
I am with you on that Dennis, I too (though I am also lazy) believe that the odd imperfections are part of me, somewhat in the vein of the Arts and Crafts folk, I really do not want my stuff having a manufactured look.
-
I adore Dennis' texturing and have on his very good advice, textured the backs of my last two brooches with this frosting wheel!
Cookies have a kit of radial wheels (not sure if they're lookalike 3M) which are good value. For firestain I also like the silicon knife-edge wheels. The pink one is a final finish quality, only exceeded by Luxi white.
-
How do you use the silicon knife edge wheels Joe?? I am really asking if you find you get ridges/lines from it? And any tips in removing firestain with it?! I've used other silicon wheels with reasonably good polishing results but haven't tried these.
Thanks
Tabby
-
Ah yes!!
You need to keep the wheel moving over the piece - the blue one especially cuts grooves very easily. I use the top surface usually rather than the edge - it's curved slightly and the edge flexes down to conform to the metal giving you a surface you can use:
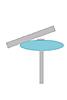
Oh, I also sand the edges of the screw smooth (rotating it on a bit of emery with no wheel in) - it can rip into the metal if it accidentally touches when used like this.
The very edge can be useful cleaning around bezels when it's sharp. Dennis, I think, had some useful advice about dressing these wheels using the cheap diamond sharpening plates from places like Poundland!
The radial wheels can be mounted several at a time on the mandrel to give a small polishing mop which is less liable to cutting grooves.
Last edited by Joe; 12-02-2011 at 10:59 AM.
-
While you're on this rubber lark, don't forget the cup shaped ones for screw mandrel (I got mine from Rashbel). The inside surface will do a good job on round bezels and the outside surface is less inclined to leave directional marks.
I am also very fond of my 3M flexible abrasive disks, grandly known as " Imperial Micro Finishing Film Sanding Disks", which came as an assortment from Rio Grande. They are safe sided plastic and can be reduced in size as required by holding a needle obliquely to the smooth side while running. The fine ones used lightly and kept moving will obliterate those annoying pallions of solder which went astray or didn't quite melt. Do you get those?
The coarser ones with practice will make swirly patterns like you see on aluminium bistro tables.
Nil Carborundum, Dennis.
-
Thank you both :-) Tomorrow's plan - research the tips and sources you've given. Joe, those discs make sense now, I had only thought of using them edge on, therefore my avoidance.
Thank you
Tabby
-
One plays with these toys to find the things that work best in one's own hands...
But... now I have to buy more stuff to try thanks to Dennis! The 3M sanding disks I already own (and have avoided), but cup-shaped rubber wheels... I need them!
Posting Permissions
- You may not post new threads
- You may not post replies
- You may not post attachments
- You may not edit your posts
-
Forum Rules
Bookmarks