-
Texture or Polish?
This might be in the wrong forum, apologies if so.
what are people's views on jewellery which has a lot of texture to the metal? Some of my bangles have small barbs and fairly rough areas. I like them but some people have said that I should make them super-smooth.
Also, the insides are almost impossible to get to a flat smooth finish unless I literally grind half the thickness away. Does it matter if there are marks from the original pattern?
-
Definitely do what you like! Appeal to lovers of your work. It is so much easier to sell the things you think are great than the things that you feel ambiguous about.
I make unusual pieces; they don't appeal to everyone but those to whom they speak simply adore them. Obviously I've seen your images in your posts and have a feeling of my own towards them - I feel that the inside and outside finishes match and a lover of one will love the other. However, I do feel that there is something a bit compromised about both finishes compared to the way (I imagine) the original organic circlets look: they are a little soft and some detail has been lost in finishing.
Practically, you need to worry a bit about snagging and injury and discomfort... for something worn against the skin like your bangles, you need to make sure that customers want to wear them. But for a statement piece, people will put up with discomfort, so there's no real limit.
I personally feel, as a maker of art-jewellery, that you should be as true as possible to your vision and sell that - barbs and all - to the people who fall in love with them.
-
the detail isn't so much lost in the finishing as in the casting sometimes. I have to give them a wax coating to keep the seaweed together and also because when it dries out, it's absolutely razor sharp, so I do somewhat soften some of them in that way.
I have three pieces which fit into the "statement' piece...
this one...


and this one... (bad pics and they don't have the pearls in yet)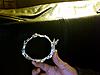
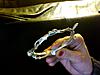
as you can see, they literally have barbs on them. I suppose it's a crisis of confidence. I want people to like and buy my stuff, but I don't want to compromise too much.
-
That's just what I mean - a sort of marmite thing I suppose... if you love it, you love it; if you don't then polishing down the curious, organic details won't help!
I have a lovely etching on my wall made by a friend; the only edition from a large plate that didn't work out. The lines are muddy; the tone dark; the milieu sombre. But it is actually a fun image full of complexity and fantasy and opportunity for one's own imagination. I adore it. Though she frets about the flaws so much that she won't make another edition, we see the same thing in the image and she asks after it when we meet, as a feeling shared.
This is different from pretty pendant or a well-executed setting. There is depth in art and execution is only part of the equation: it must be adequate, it should be competent, it need not be conformant.
I acknowledge that mass-appeal is important to commercial success and I am (as she) working on higher volume pieces which are only touched by the feeling of the art pieces but intended to be offered for sale alongside.
I can't approve of the barbed hooks and the feeling that they might catch and snag and I would take my graver to the pitting... but that just means they don't catch and snag my adoration, though I can see that they are exciting, unique pieces! Others will see in them what you see.
Maybe hammer-out some plain offerings to run alongside these, but sell your heart and spirit in these pieces too!
-
It's a tricky one. I agree with what's been said but I know that if I don't soften every corner on my work, people won't buy it. It's all very well saying "it's art" but people usually buy jewellery to wear it rather than to put it in a cabinet. I've adopted a very commercial style over the years as I need to make a living from it. Maybe I've sold my soul but a girl's gotta eat.
I don't have my work cast (though it's something I think about from time to time) but I was wondering whether when you wax coat your seaweed, you could smooth off the inside in any way?
-
Joe,
I suppose the repro enamelled stuff is where the bread and butter will be coming from once I get under way. I know that my seaweed doo dahs only appeal to a fairly niche group but I don't want anyone put off because of the potential for scratch.
on a technical note, can you elaborate about using a graver to clear out the pits? that is something that does bug me!
Carole, absolutely everyone has to eat though I wonder if you have more created a desirable style than a commercial one? the two aren't mutually exclusive and your work is far from bland IMO.
When I wax coat my seaweeds, the insides are actually very smooth, but what happens when they cast is that behind that smoothness you get voids. it's because the seaweed is slightly explosive and doesn't disappear when the cask is fired. So when I get them back and start to clean them up I get bits breaking off. fortunately it seems more of an issue on the inside of the bangles than on the outside, though the fucus above is pretty flaky all over. It's one reason why I cast them. It means the cast of the cast is actually solid. If I grind and file down the inner surface on the first cast one, there is a danger that it might break apart, and on the subsequent casts, I could be grinding away grams of silver and I kind of think that it's better to have the silver on the bangle than on the floor as long as the inside is smooth and not having any sharp edges etc. what I could do, thinking about it, is maybe fill the voids on the first cast with solder, so when the mould is made it's got a smoother surface?
-
Hi Liz,
If I was making your seaweed bangles, I would have the first cast in copper, then I would clean up the copper master pattern, filling in any unwanted pits and holes, then I would use this to create the mould for the silver bangles. This was the method I used when copying the lion of the UK parliament Black Rod, I made a wax model first then got it cast in copper so that I could perfect the master pattern before getting it cast in silver. I made the new Black Rod for the parliament of NSW many years ago. Also do you use Cratex rubber grinding wheels, as they come in all grades and are great for cleaning castings. For cleaning out casting pit holes I would use diamond burs, here is a nice bargain set on Amazon; http://www.amazon.co.uk/Toolzone-30P...9072002&sr=8-6
James
-
Hi, I don't really have anything very helpful to add from a technical point of view.... but I just wanted to say that I LOVE, LOVE, LOVE, that bangle.
-
Hi James,
I use the cratex tips, haven't seen the casting wheels. I hadn't thought about using copper. I assume my caster will do copper. The smaller christening bangles are one offs and so far, they have cast ok directly into silver. Probably because they are so small. If I clean out the pit holes on the existing castings, do you think it matters very much if I leave them as pits on the ones i already have? Some people who have seen them think that the pits are ok because it's part of the character, but I feel it might be better if they were smoother.
Sometimes I get paralysed by having to make decisions!
ETA: thanks, Fay!
-
Hi Liz, Cookson sell their own type of Cratex wheels called Eveflex, they are available in course grades for grinding and finer grades for polishing. Diamond burs are useful , the ball burs are great for cleaning out pit holes and the straight burs are good for adding textures. Most casters will cast in copper alloys. I have used Niagara Falls Casting in the past and they will cast in gilding metal which is a copper alloy. Below is one of my wax models cast in silver by Niagara falls Casting.
James
Posting Permissions
- You may not post new threads
- You may not post replies
- You may not post attachments
- You may not edit your posts
-
Forum Rules
Bookmarks