-
Gauge of Back plates
Hi everyone, I've been making gemstone backplates for pendants and rings in 0.5mm sterling silver sheet for some time now. I'm interested to know what everyone's favourite gauge mm is for this task. For the bezel more often than not I'm using 0.4mm fine silver. I'm pretty sure that was Dennis' recommendation on this forum. Thanks Dennis
-
Hi Sheena,
Much depends on the size of the stones: a 3.0 mm stone can happily survive on a 0.5mm backplate.
For a 15.0mm stone, it would be a bit flimsy.
Also for a pendant there is much less strain on the metal backplate. For a ring the shank is connected there, so it is subject to much more twisting and banging when in use.
I know you like rules, but in the end you will have to use judgement, or take time out to test some pieces to destruction.
Kind regards, Dennis.
Last edited by Dennis; 15-11-2023 at 09:34 AM.
-
Thanks Dennis, I've just been given a ring commision which involves a 3 1/2 cm by 2 1/2cm carnelian cabochon in an open backed setting. I was thinking of maybe using 0.8mm silver sheet for the backplate. It's a bit of a guess as I've never made anything that big before.
-
Yes, that feels about right to me too Sheena. Quite a statement ring. Dennis
-
That’s what I would use too
-
It occurred to me that a large ring like that needs gentle application of a large torch, possibly in a darkened area, for fear of melting the bezel material.
You might consider a slightly thicker bezel, say 0.5mm, soldered onto the backing with easy solder, and then onto the shank with extra easy. Do not quench as that might cause it to distort, but allow to air cool.
Practice with copper first to understand the snags. Let us know how you get on, Dennis.
-
I was going to practice on copper as I've never used 0.8mm silver for a backplate but when it came down to it I was too impatient. I woke this morning and just wanted to have a go. As it turned out the bezel soldered to the backplate like a dream. Previous times using 0.5mm it's difficult to get a large piece up to heat and not overheat. 0.8mm was much easier getting up to heat evenly. Next up is to solder on three tube settings.
-
If your screen is fogging up, it' because we are watching with baited breath.
-
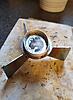
This was my soldering set up with the titanium trivet from cookson
-
She wants a shank like this. Tried it out in copper first to see if it was do-able.
Posting Permissions
- You may not post new threads
- You may not post replies
- You may not post attachments
- You may not edit your posts
-
Forum Rules
Bookmarks